Pokročilá laserová technologie zajišťuje vysokorychlostní přesné spojování nezbytné pro hospodárnou výrobu bateriových článků pro elektromobily.
Konstrukce a výroba válcových baterií větších rozměrů pro elektromobily slibuje výrobcům automobilů i spotřebitelům několik výhod. Pro řidiče jsou to například větší dojezd, vyšší výkon, rychlejší nabíjení, delší životnost bateriových článků a lepší provoz v chladném počasí. Výrobci se mohou těšit na zefektivnění výroby a snížení výrobních nákladů.
Co je na výrobě baterií pro elektromobily tak složitého?
Různí výrobci se zabývají řadou různých konstrukcí válcových baterií velkých rozměrů. Každá konstrukce a pracovní postup představuje vlastní specifické výrobní výzvy, zejména pokud jde o procesy spojování. Například některé konstrukce baterií pro elektromobily obsahují sběrače proudu a ty musí být spojeny s válcem galvanického materiálu s velmi přesnou kontrolou hloubky svaru. To je nezbytné, aby nedošlo k poškození separátorů, což by mohlo následně vést ke zkratu uvnitř článku. Podobně i svařování svorek s kolektorem vyžaduje pečlivou kontrolu penetrace. Zvláště důležité je omezit množství tepla, které se při této operaci do baterie přivádí, protože by mohlo dojít k roztavení nebo poškození polymerních izolátorů.
Dalším procesem spojování, který byl v minulosti úspěšně používán u baterií menších rozměrů pro utěsňování víček je mechanické lisování. Krimpování se však pro větší články příliš nehodí a je zapotřebí nový přístup.
Jaké jsou současné požadavky?
Při výrobě baterií existuje řada svařovacích procesů, které se opět liší podle výrobce a konstrukce. Všechny nejnáročnější a nejcitlivější z nich však mají určité společné požadavky, včetně potřeby:
- Minimální tepelně ovlivněná zóna
- Přesná kontrola hloubky průvaru
- Eliminace rozstřiku materiálu
- Vysoká rychlost procesu, obvykle v rozmezí 200-500 mm/s
Navíc některé důležité procesy spojování baterií vyžadují také svařování nepodobných kovů.
Každý z těchto požadavků představoval v minulosti obtíž a ve skutečnosti neexistovala jediná technologie svařování, která by dokázala dobře fungovat ve všech procesech. Výrobci proto hledali různá řešení. Patří mezi ně lasery se zelenou vlnovou délkou pro svařování mědi (aby se překonala nízká absorpce tohoto materiálu infračervenými zdroji) a nelaserové metody, jako je ultrazvukové svařování pro spojování foil-to-tab.
Vybavte se správným laserem
Společnost Coherent vyvinula nový typ laseru, který má širší využití než cokoli předtím. To je možné díky tomu, že tato technologie poskytuje bezprecedentní míru kontroly nad tím, jak je laserová energie dodávána na pracovní povrch - jak z hlediska prostorového rozložení, tak i v čase.
Klíčovou inovací je technologie Adjustable Ring Mode (ARM) - vláknový laser, jehož paprsek se skládá z centrálního bodu obklopeného dalším soustředným prstencem laserového světla, na rozdíl od tradičního výstupu s jedním bodem. Nejdůležitější je, že výkon ve středovém a prstencovém bodě lze nezávisle řídit, a dokonce i modulovat. Graf ukazuje, jak tento přístup přináší obrovskou flexibilitu v tom, jak přesně je laserová energie během svařování distribuována.

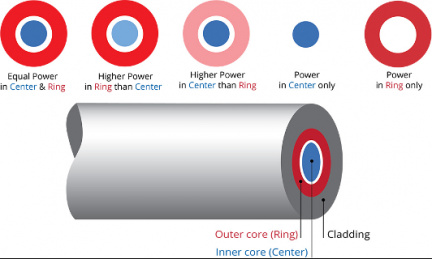
Obrázek: Základní výkonové vzory zaměřeného bodu FL-ARM.
Výhodou technologie ARM je, že umožňuje velmi přesné řízení dynamiky taveniny. To umožňuje konzistentnější a kontrolovatelnější zpracování a prakticky eliminuje rozstřikování materiálu. Tento typ laseru je obzvláště užitečný pro svařování mědi, protože kruhový paprsek lze použít k předehřátí materiálu, což podstatně zvyšuje jeho absorpci infračerveného světla při následném zpracování. Středový paprsek s vysokou hustotou výkonu zajišťuje vysokou absorpci infračerveného laserového paprsku mědí. Spolu s praktickými a cenovými výhodami vláknových laserů to z vláknového laseru ARM činí velmi atraktivní alternativu k zeleným pevnolátkovým laserům pro svařování mědi.
Jediný typ laserového zdroje, který dokáže plnit tolik různých úkolů, poskytuje výrobcům větší flexibilitu a hospodárnost. Například výstup z jednoho laseru lze sdílet mezi více procesů pomocí přepínačů paprsků. To zefektivňuje a zjednodušuje výrobu. Použití společného typu laseru na více místech výrobního procesu také snižuje zásoby náhradních dílů a poskytuje redundanci, která pomáhá minimalizovat prostoje při údržbě nebo opravách.
Více o vláknových laserech COHERENT HighLight ARM naleznete na optix.cz